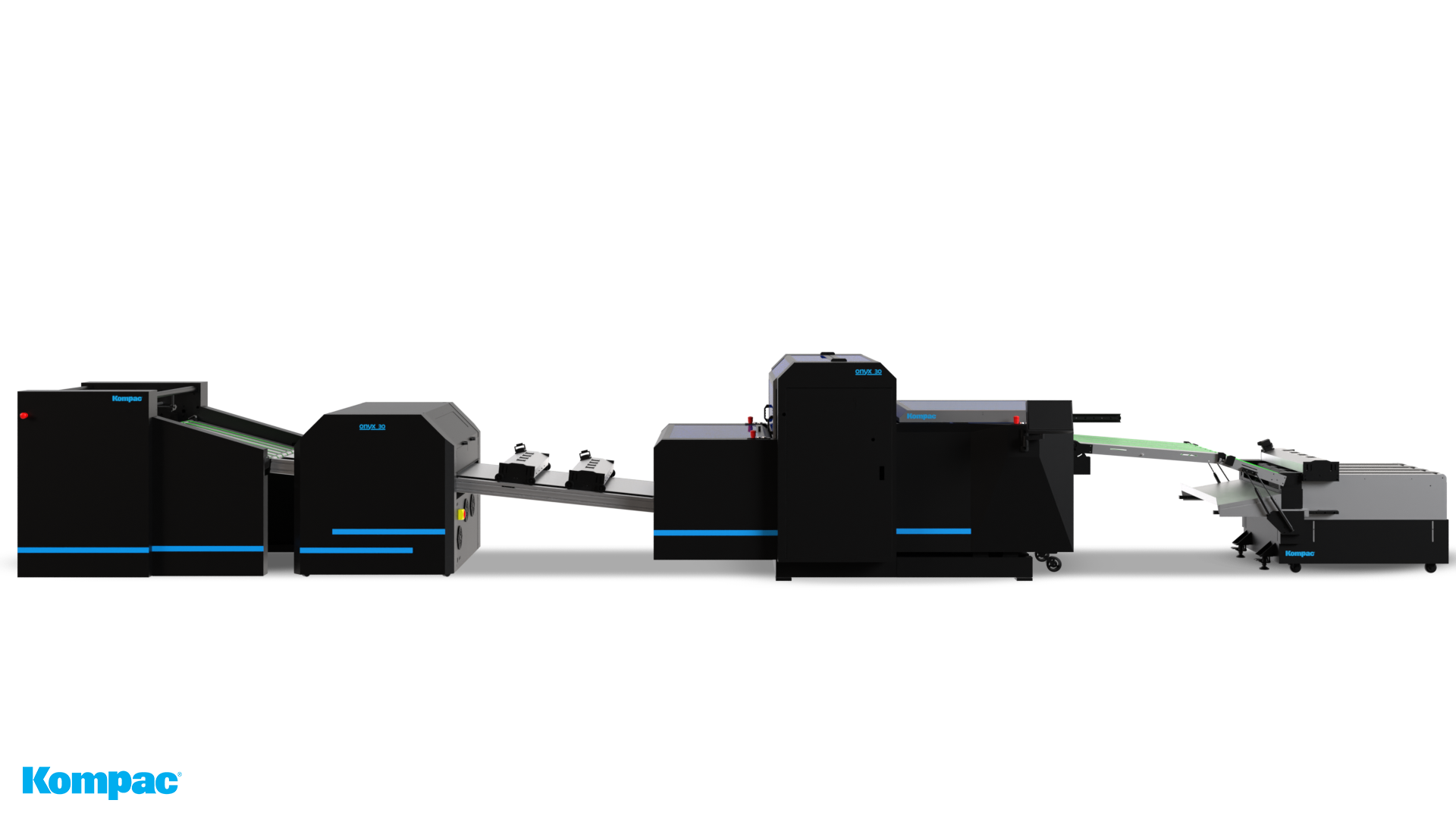
Introducing the Kompac Onyx 30i Inline Spot/Flood UV/AQ Coating System
The Kompac Onyx 30i in-line flood/spot coating system is making waves in the printing industry, offering a seamless way to apply UV/AQ coatings and specialty finishes to various substrates. Designed for efficiency, this cutting-edge machine caters to B2 or smaller-sized sheets, accommodating everything from lightweight text paper to robust card stock, all in a single pass.
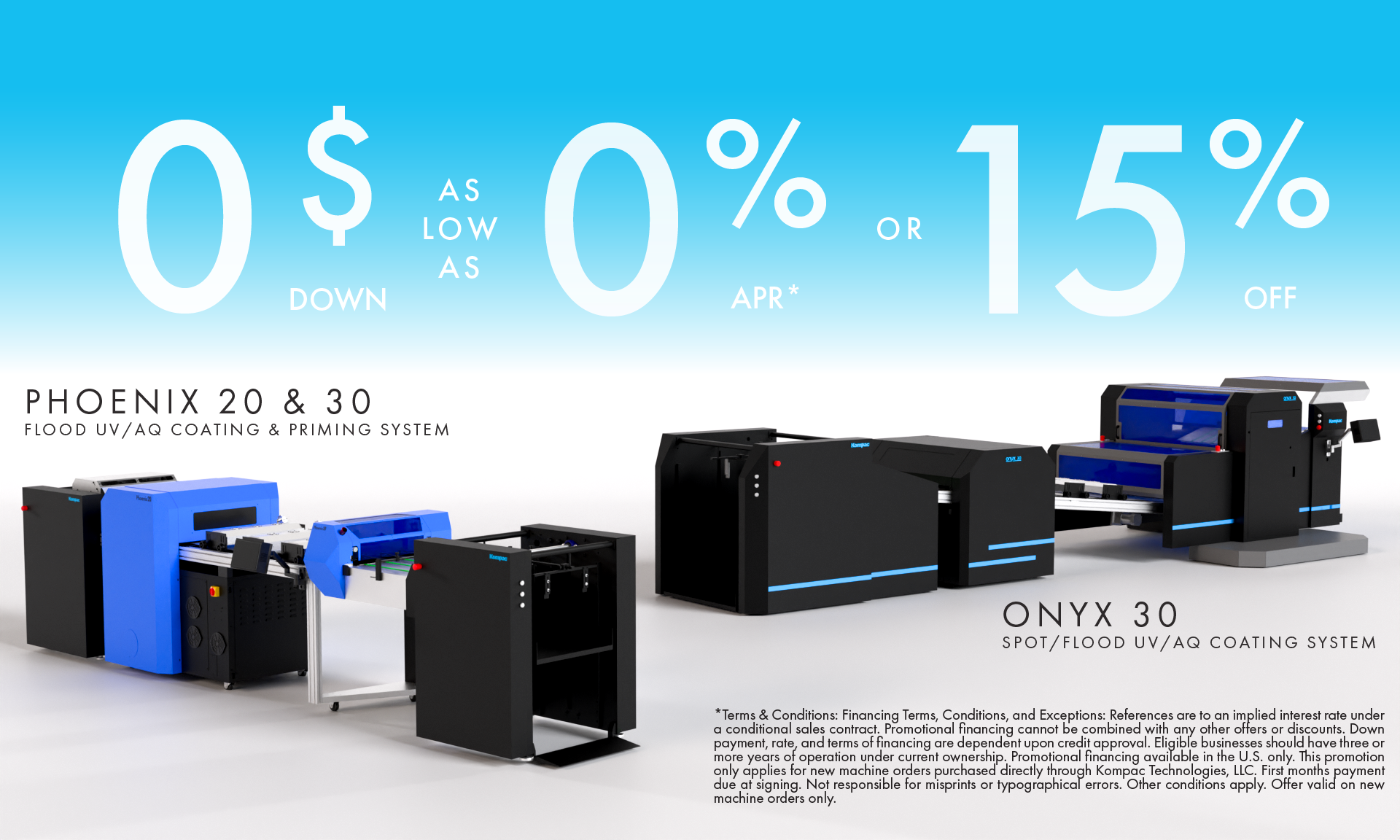
Kompac Summer Financing Event
Discover the flexibility of our modular design, easily configurable for sheet, web, inline, or nearline applications. Choose from UV, IR, or NIR drying options, with up to four IR units available for pre or post-coating configurations. Our system supports multiple coating setups, including up to four anilox or standard coating units per system. Benefit from variable length conveying for optimal wet-out or additional curing time, and achieve high-speed performance at up to 250 feet (76 meters) per minute. Powered by the Kompac IOTech4 network platform, it enhances efficiency and accelerates job turnaround. Proudly made in the USA.
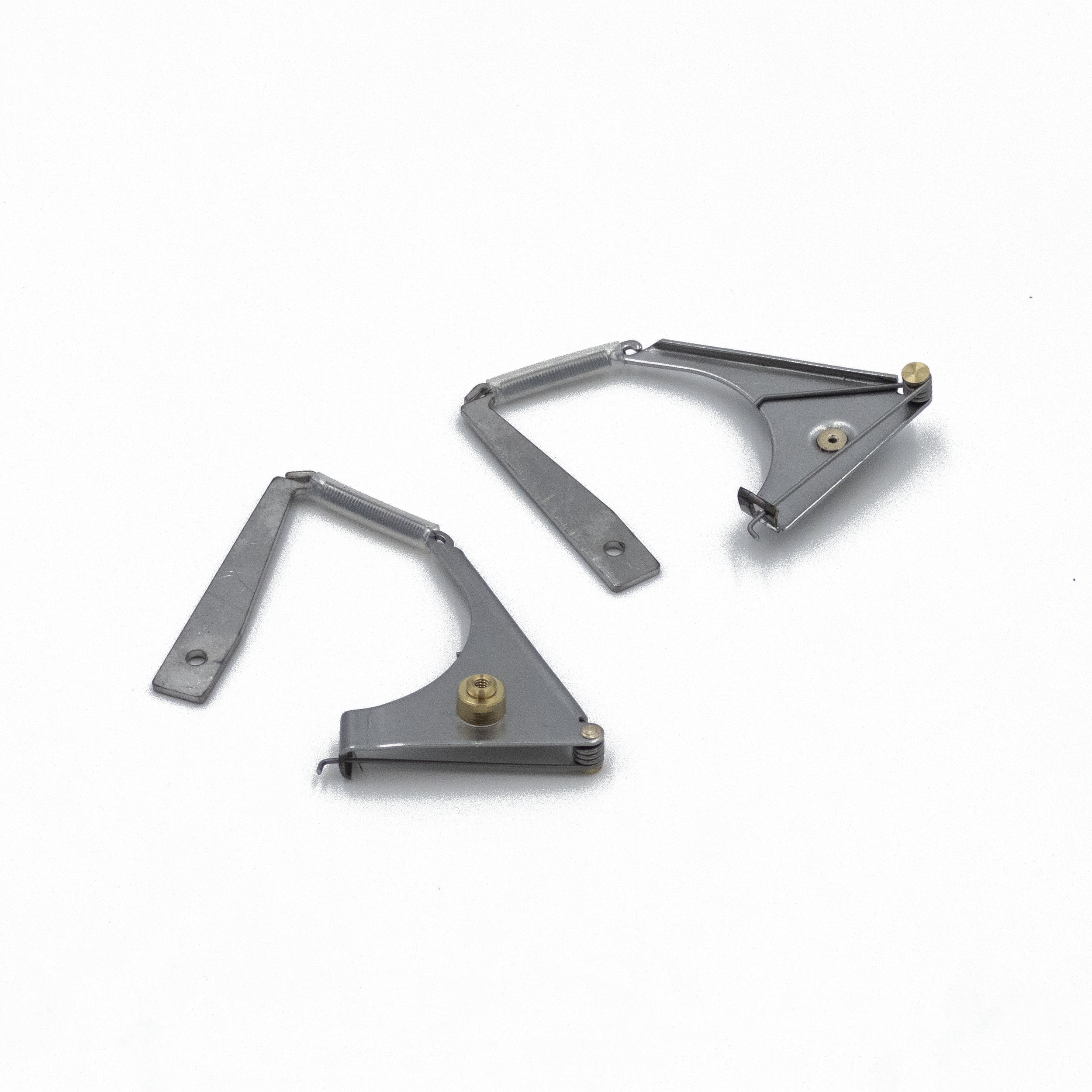
Genuine Kompac Parts for Your Kompac Coater
When it comes to keeping your Kompac coater in top condition, always opt for genuine Kompac parts. Your investment in these parts will pay off in the form of reliable performance, lower maintenance costs, and peace of mind knowing that your warranty remains intact. For the best results and to protect your equipment, make the choice for quality and trustworthiness by using genuine Kompac parts for all your maintenance and repair needs.
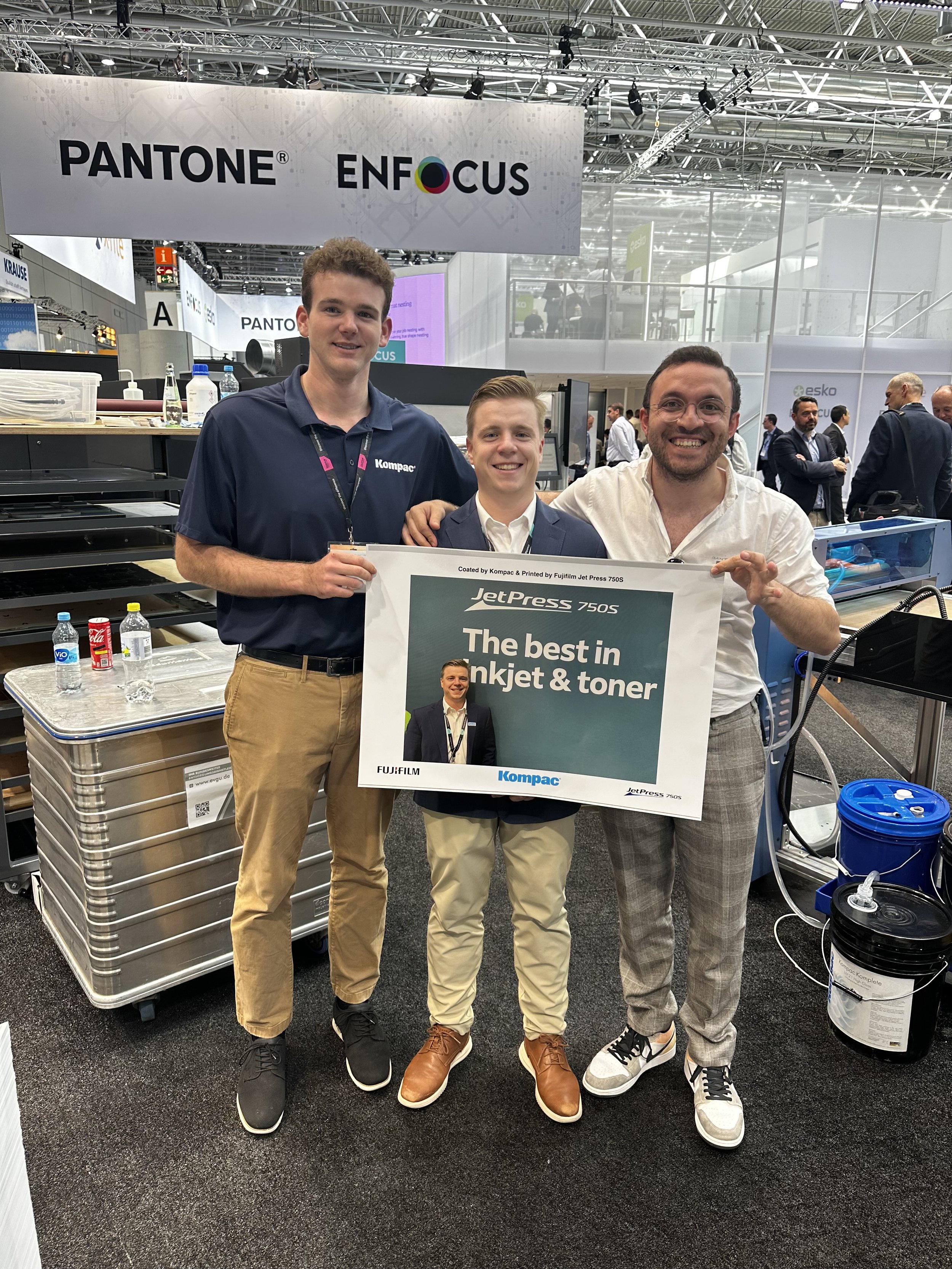
Thank you from Kompac!
Drupa 2024 was an incredible experience from start to finish. I want to express my heartfelt gratitude to our esteemed partners at FUJIFILM and TECNAU for hosting us in their booth. The enthusiasm and engagement at both booths were truly remarkable. At the FUJIFILM booth, there was a constant stream of visitors eager to learn about the Jet Press 750HS and the Kompac Phoenix 20. These integrated machines offer a seamless solution that print and packaging companies will find immensely valuable.
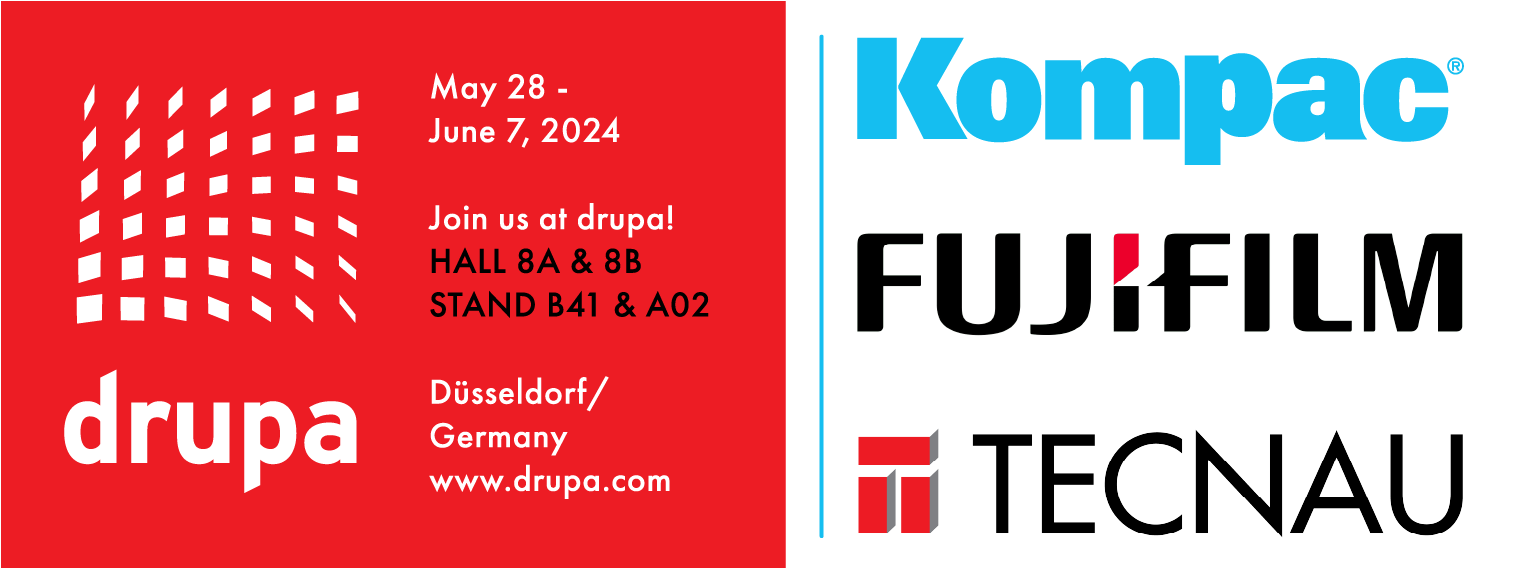
Come see Kompac with Fujifilm & Tecnau at Drupa 2024!
Kompac will be at Drupa from May 28 - June 7, 2024. Kompac will be featuring 2 of our Phoenix machines in two different booths. Kompac will have a Phoenix 20 inline with a Tecnau Stack1212 in booth B41 in hall 8A. Kompac also will be showing a Phoenix 30 inline with a Fujifilm J Press 750 and that will be in booth A02 hall 8B. Come see our machines run inline and Kompac will also have samples including spot jobs and di-cut jobs that have been run on the Onyx 30.
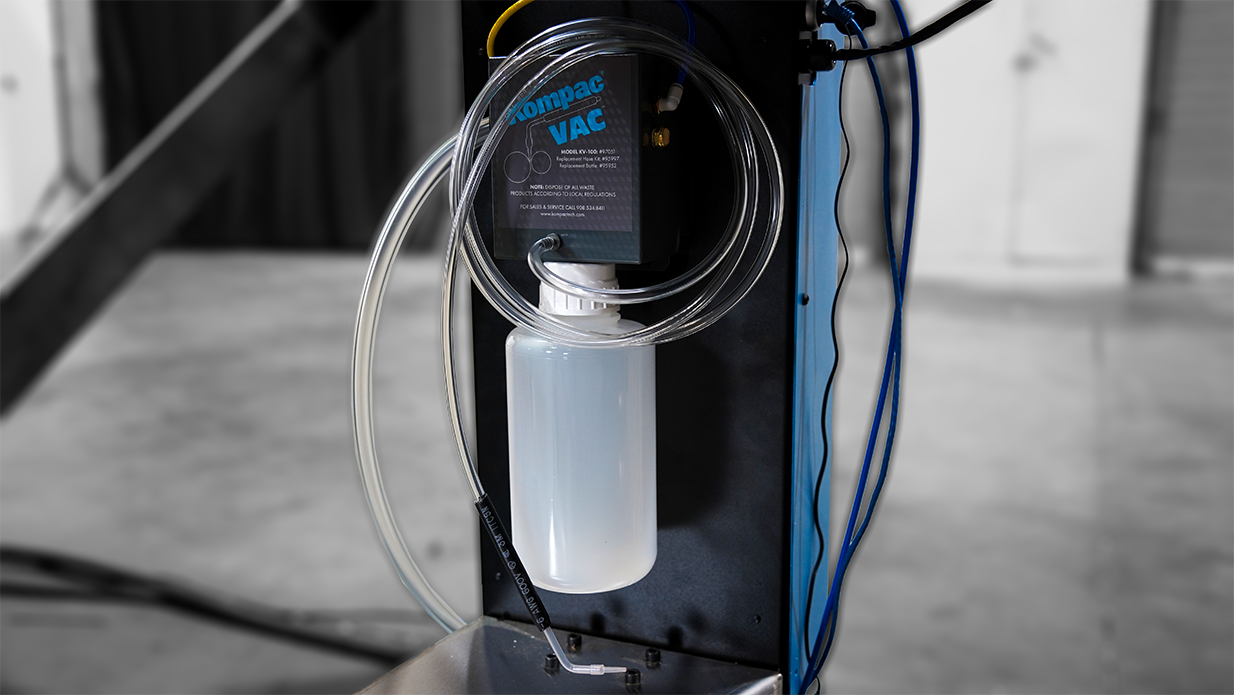
Kompac Vac: You Solution to UV & AQ Clean up
Kompac Technologies has a patented cleaning system that is the fastest, easiest and cheapest on the market. Say goodbye to spending a bunch of money on cleaner and wasting 45 minutes to clean a machine. The Kompac Vac will take no longer than 2 minutes when cleaning up UV or AQ coatings.
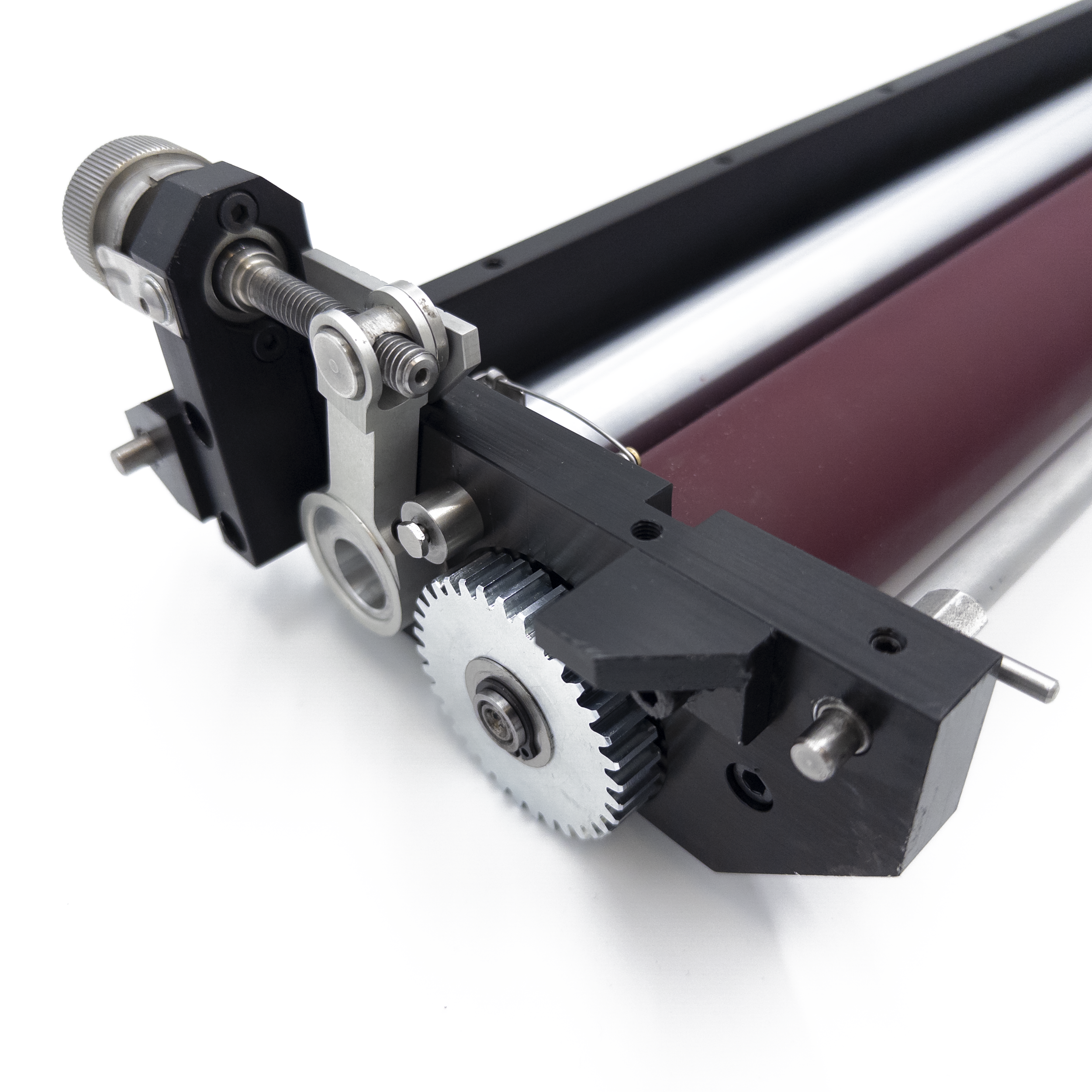
Introducing the Kompac Kwik Change: A Quantum Leap in Printing Efficiency
Kompac Technologies is excited to introduce a game-changing innovation that is set to transform the world of printing: the Kompac Kwik Change. Say goodbye to prolonged downtime and tedious recalibrations – this groundbreaking advancement promises to revolutionize the way you approach printing assemblies.
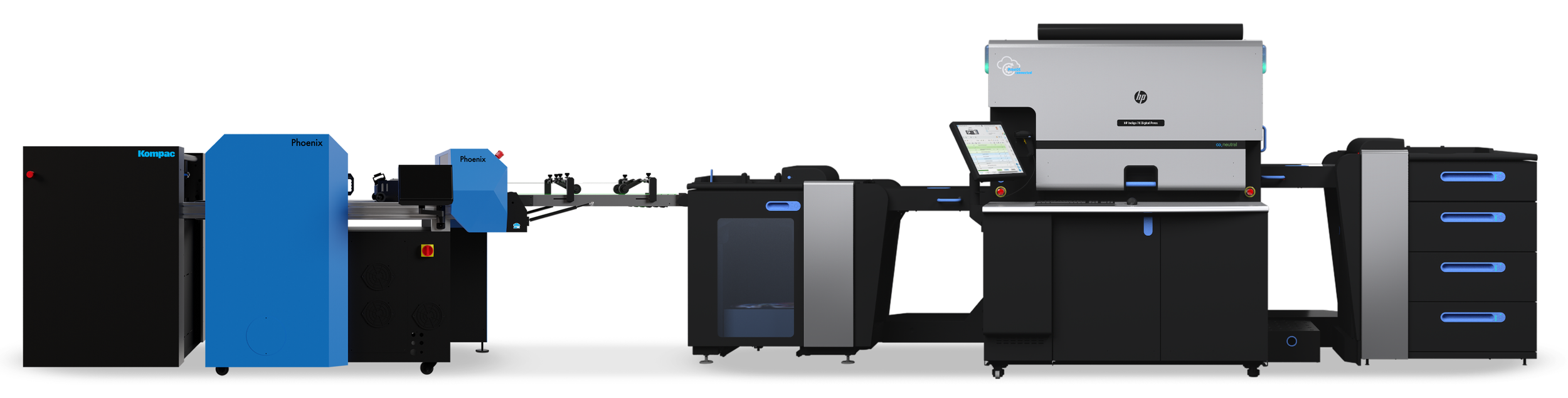
Kompac & HP: Phoenix In-Line UV/AQ Coating & Priming System
The Phoenix coating system provides exceptional flexibility, allowing configuration in either in-line or nearline setups and in simplex or duplex modes. Its modular design empowers customers to customize the equipment to precisely match their business requirements, making it an ideal solution for businesses aiming to enhance operational efficiency. Utilizing Kompac’s distinctive UV or Aqueous coatings, the Phoenix allows users to attain precise flood coating on various substrates, emphasizing ease of operation and cost efficiency. Moreover, the Phoenix is seamlessly compatible with HP Indigo Digital Presses, ensuring a harmonious integration for a comprehensive and efficient printing experience.